Why should a 118-degree conical hole be drilled at the end when the power head drills a blind hole?
2022-11-21
Copyright belongs to the author. For commercial reprint, please contact the author for authorization, for non-commercial reprint, please indicate the source.
Let me talk about the conclusion first. The power head drill bit with an angle of roughly 118° has good performance in drilling most materials. However, considering the convenience of production and design of the drill bit, 118° was selected because the tangent value of 59° is relatively close to 0.6, which is easy to calculate. Measurement. 120° is just an intuitive round, but trigonometric functions are not linear.
I didn't want to answer questions about power head processing and drilling machine design. After all, it's not my current direction. Many people who don't understand need to check the information. But seeing the perfunctoryness of other answers, I think it is still necessary to answer. And this question is very interesting and complicated.
One point mentioned in other answers: the angle of the top angle of the blind hole is determined by the drill bit with a top angle of 118°. This is correct. Therefore, the subject's question can be transformed into: Why is the apex angle of the twist drill 118° instead of 120°? Several other answers did not continue to explain, which is the same as not answering.
First, the "standard theoretical perspective" is not a convincing answer. When introducing the history of twist drills in Wikipedia, it is mentioned: "The most common twist drill bit (sold in general hardware stores) has a point angle of 118 degrees, acceptable for use in wood, metal, plastic, and most other materials, although it does not perform as well as using the optimum angle for each material. In most materials it does not tend to wander or dig in.” That is to say, when the power head drills most materials, the performance of the 118° drill tip angle is the best. Similar to the performance of the optimal vertex angle for each material. Therefore, it is unified to 118° in many cases. Moreover, the twist drill was invented in 1861, and the 118° drill bit apex angle was included in the standard in 1920. At that time, there were no computers and no finite element analysis. Maybe the measurement methods did not support enough understanding of the drilling process, so an optimal theoretical angle was calculated. It must have been unrealistic in those days.
Since the performance gap is not large, the unified apex angle standard can greatly simplify the complexity of manufacturing drills and drilling processes. But why not choose 120°? The following answer is explained from the perspective of production drills, and I think it makes sense:
”118 vs. a round number like 120, as both are close to the optimum compromise for commonly drilled metals of the day, one will note 1/tan (59 deg) = 0.601 (essentially 0.60) whereas 1/tan (60) = 0.577…
If you multiply the radius of the drill by 0.6 (or, easier, the diameter by 0.3) you get the length of the conic tip in a blind hole to within 0.014% eg within 0.0002″ for a 1/2″ dia drill. to calculate w/oa calculator, while the functional difference was trivial. OTOH, in manual drafting, the cone angle would be drawn using a 30-60 triangle, as no one was going to scale the drawing for the exact value.” Why 118? Why 135? (Drill angle)
That is to say, although 120° looks more rounded than 118°, tan(59°)=0.601 can be approximated to 0.60, while tan(60°)=0.577, the error of approximating 0.60 is relatively large. When producing and testing drill bits, it is obviously easier to calculate and measure the drill tip height and drill diameter of the drill than to measure the apex angle.
But not all twist drills have a top angle of 118°. The more commonly used ones are 118° and 135°. There are also various angles. After all, the level of technology has improved, and it is no longer difficult to produce drills with different angles:
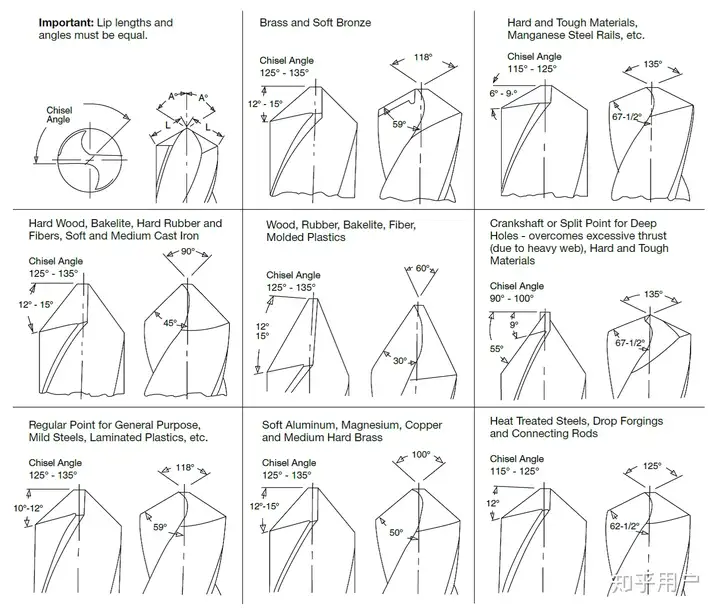
Moreover, not all blind holes will have vertex angles. An extreme example is the use of electroplated diamond drill bits, which can be used to process blind holes in ceramic and glass materials:
